Milling capacity increased with the addition of a Loesch Mill.
OUR OPERATIONS
Idwala Carbonates
Idwala Carbonates mines a deposit of unique super white calcitic and dolomitic limestone
This limestone provides the raw material for our range of fine carbonate products. Situated on the Umzimkulu River near Port Shepstone on the Kwa Zulu Natal south coast, Idwala Carbonates extracts some of the whitest carbonates in the world.
<
0
Tons Processed
0
%
Purity
0
% Ry
Brightness
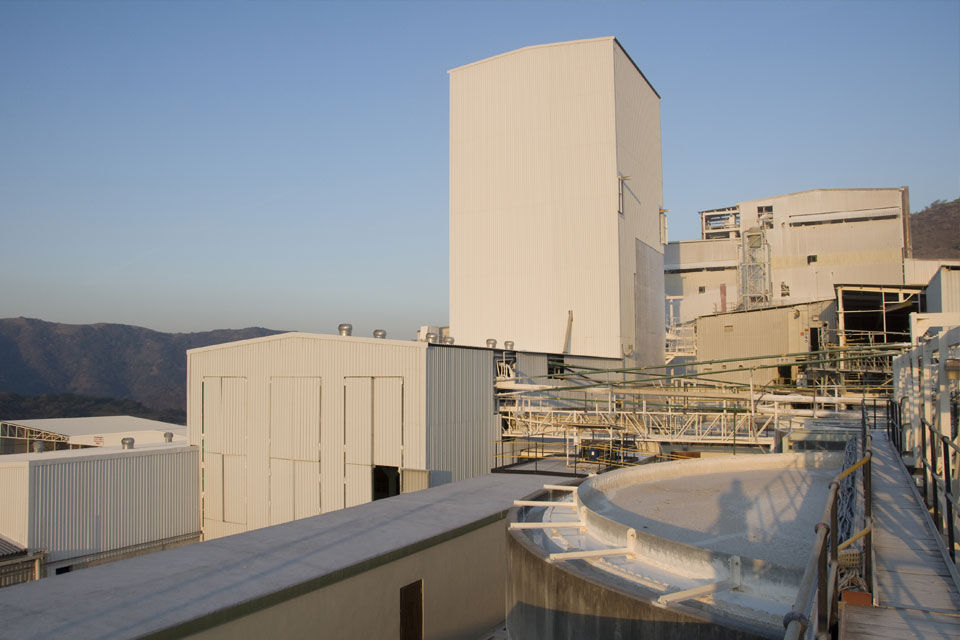
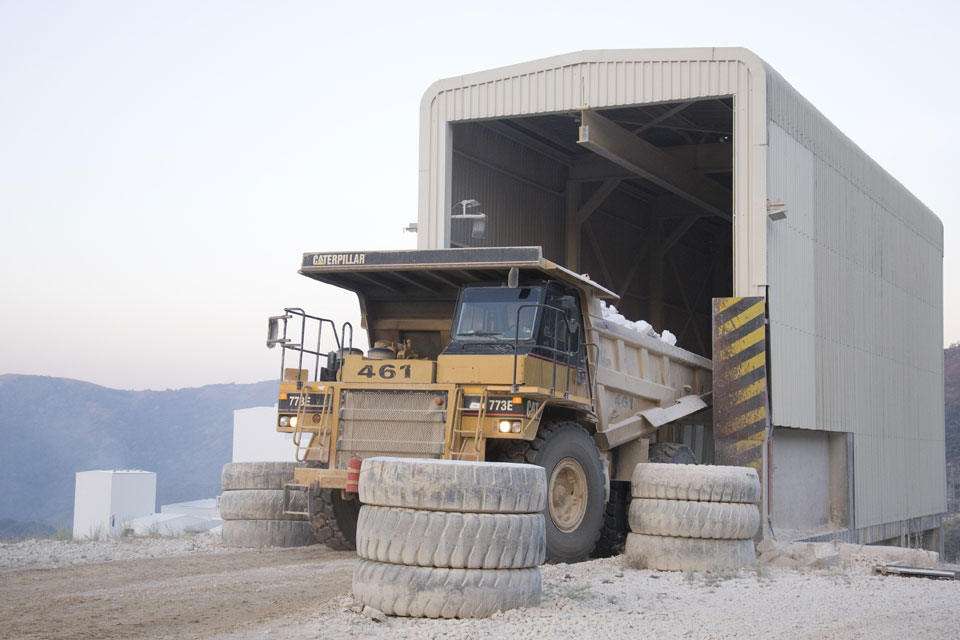
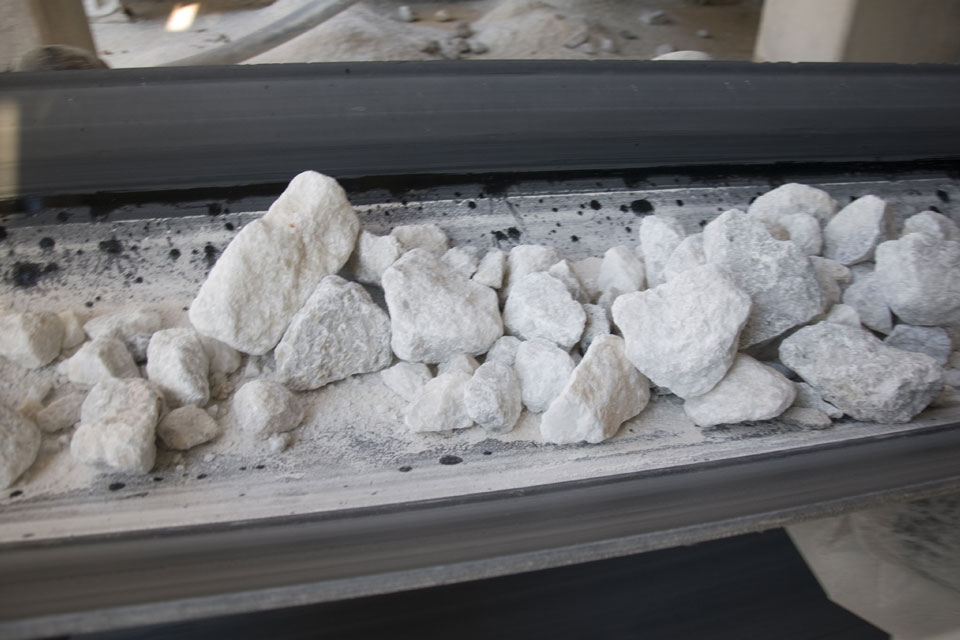
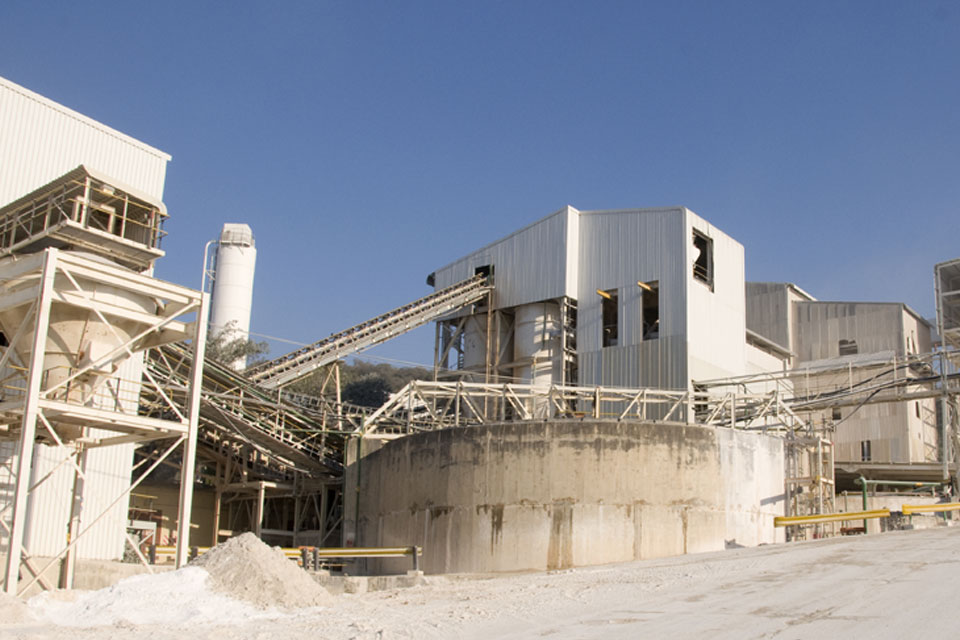
Idwala Carbonates mines a deposit of unique super white calcitic and dolomitic limestone which provides the raw material for our range of coarse milled to fine carbonate products. Situated on the Umzimkulu River near Port Shepstone on the Kwa Zulu Natal south coast, Idwala Carbonates extracts some of the whitest and purest carbonates in the world. The deposit consists of coarse-grained Calcitic and Dolomitic Marble and the mine is located approximately 20 km’s from Port Shepstone. It covers an area of approximately 10 km² of the Marble Delta Formation and is known as the Simuma Complex.
The commodities produced range in micron sizes produced from both Calcitic and Dolomitic stone. The Calcitic grades range from a 50mm stone, 5mm prills to 200, 40, 15, 10, 5, and 2 um powders. The Dolomitic grades range from 5 mm prills to 200um powders. The application of these products is found in most industrial, pharmaceutical and farming processes. The operation includes an efficient, technically advanced process which produces our beneficiated range of carbonates under the Kulubrite name for use in the manufacture of paper, paint, plastics, ceramics and chemicals.
The production process begins with the quarrying of the raw limestone which is then taken through two stages of crushing to reduce it to small, manageable rocks. This material is scrubbed and washed to remove surface clay and dust before being sent through a third crushing process to further reduce it to granules. Up to this stage in the production process the product is unfloated and ranges in mean particle size from 15 micron to larger granules.
This granulated material is processed through a floatation plant where non carbonates are removed, thereby improving the chemical quality and colour of the product. This floated product which is in filter cake form is dried using flash dryers. The dried product is finally milled and classified to produce powders of various particle size distributions, ranging in mean particle size from 1 micron to 45 microns. These super-white, superfine powders are stored in silos, awaiting either packaging or bulk distribution to customers as our Kulubrite range of products.
At every stage of the production process the material is subject to rigorous quality control with the final product being tested with state-of-the-art analytical technologies. This ensures that the unique quality and colour characteristics of the raw resources are preserved to produce a world-class product on which our customers know they can rely on.
1946
SA Quarry Industries was established on the site that is now known as Idwala Carbonates.
1950s
The Carbonates operation was bought by cement producer Anglo Alpha.
1959
The Hill Plant was commissioned for aggregates.
1979
Phase 1 of the Valley Plant commenced.
1989
The first floatation plant was commissioned to improve colour in the beneficiation process.
1996
Anglo Alpha changed to Alpha Group and the operation was re-named Alpha Carbonates.
1998
Alpha Carbonates changed its name to Idwala Carbonates with the sale of Alpha Industrial Divisions to Idwala Industrial Holdings Limited.
2001
Milling capacity increased with the addition of a Horizontal Ball Mill.
2002
Primary Mill for Unfloated Products was commissioned.
2003
ISO 14001 accreditation registered on 9 May 2003.
Moved from Disk Drying to Electric Flash Dryers.
2005
Increased floatation capacity with the third Flotation Plant.
2007-2011
Screening Plants re-located from the Hill Plant to the Valley Plant.
2006
Milling capacity increased with the addition of a Horizontal Ball Mill.
2008
Blending Plant
2011-2012
Blending Plant
2017
2019
Prills plant was commissioned
2020
Floatation agent change into ferroflote for the improvement VR for cable industry
2022
introduction of lupromin as a floatation agent to accommodate the pharmaceutical industry
2022
introduction of a new prill composite product KuluGyp
2023
Ore Sorter was commissioned
2024
addition of Food grade products